AUGUST 21, 2024
Forklift Use Guide in Dense Warehouse Environments
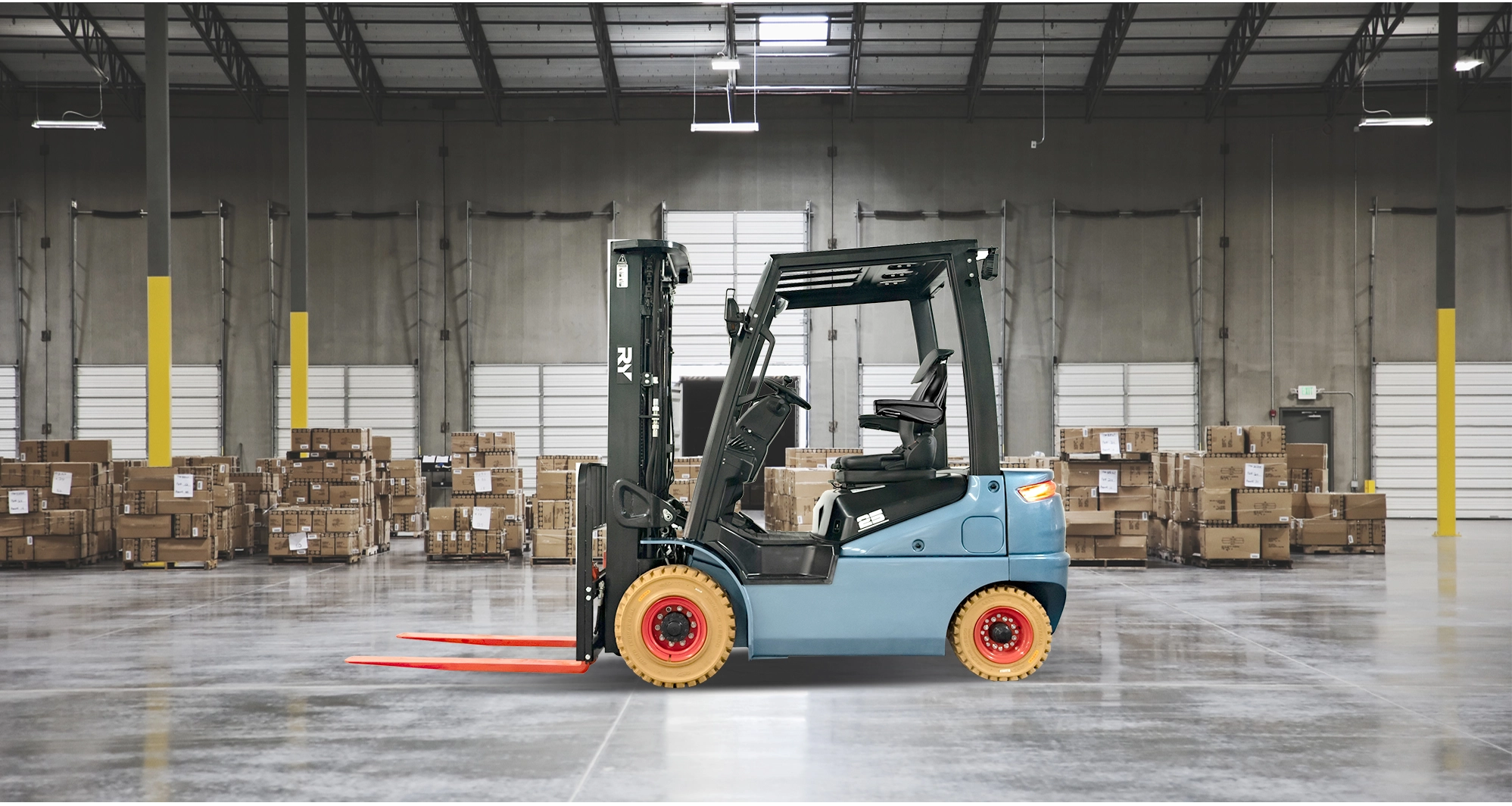
Moving forklifts in a dense warehouse environment requires a combination of skill, awareness, and strategic planning. Forklifts are essential for moving goods, but in a tight space, there are several factors to consider to ensure both efficiency and safety. Here are some key tips for moving forklifts in a dense warehouse:
1. Plan Your Route
• Identify Pathways: Before moving a forklift, identify clear, unobstructed pathways. In dense environments, aisles may be narrow, so it's important to know where to turn and how much space you have.
• Keep Aisles Clear: Ensure that aisles remain clear of clutter, whether it’s from pallets, products, or equipment. This allows forklifts to move without obstruction and prevents delays.
• Avoid Blind Spots: If the forklift has a mast or load obstructing your view, take extra care when moving through narrow areas. Slow down and ensure the way is clear before proceeding.
2. Use the Correct Type of Forklift
• Narrow-Aisle Forklifts: If you’re dealing with a warehouse that has extremely tight spaces, consider using narrow-aisle forklifts (also called reach trucks or order pickers), designed specifically for confined areas. These forklifts are smaller and more maneuverable, enabling easy navigation through tight aisles.
• Electric Forklifts: In warehouses with dense shelving or stacked goods, electric forklifts tend to be quieter, more precise, and often smaller, which can help maneuver more efficiently in tight spaces.
3. Use Proper Forklift Handling Techniques
• Drive Slowly and Carefully: In tight spaces, it’s essential to move the forklift at a reduced speed. Avoid rushing, especially when turning or navigating narrow aisles, as this can increase the risk of accidents. Slow, controlled movements allow you to adjust quickly to any obstacles or changes in the environment.
• Ensure Proper Load Stability: Always check that the load is securely placed on the forks and is evenly distributed. An imbalanced or improperly secured load can affect the forklift's stability, making it harder to maneuver and increasing the risk of tipping over.
• Lower the Forks When Moving: When traveling with a load, keep the forks low (just above ground level). This improves stability, prevents the load from swaying, and ensures better visibility, especially in tight aisles.
4. Use a Spotter or Safety Assistant
• Use a Spotter: In particularly tight areas where visibility is limited, it’s often a good idea to use a spotter or a safety assistant. The spotter can guide the forklift driver and ensure the path is clear, helping to avoid collisions with obstacles or personnel.
• Communicate Clearly: Use hand signals or radios to communicate effectively with the spotter, ensuring both driver and spotter are on the same page about the direction and any potential hazards.
5. Ensure Proper Lighting
• Illuminate Aisles and Pathways: In dense warehouses, lighting is essential for clear visibility. Ensure that all aisles, loading docks, and areas with heavy forklift traffic are well-lit. Poor lighting can make it difficult to spot obstacles or navigate narrow spaces safely.
• Check Lighting Regularly: Ensure the warehouse’s lighting is regularly checked and maintained. Dark or flickering lights can increase the risk of accidents.
6. Maintain Adequate Forklift Clearance
• Maintain Safe Distances: Always maintain enough clearance from shelves, walls, and other equipment. This is particularly important when turning or backing up in narrow aisles.
• Check for Overhanging Items: Be mindful of overhead clearance, especially when moving loads with the forks raised. Ensure that shelves or storage racks aren’t too low, and take care when lifting and transporting tall loads.
7. Use Technology to Help Navigate
• Automated Guided Vehicles (AGVs): In some advanced warehouse settings, automated systems or AGVs are used to navigate tight spaces. These systems can help reduce human error and improve efficiency in dense areas.
• Warehouse Management Systems (WMS): A good WMS can help optimize the placement of goods, reducing the need for unnecessary forklift movements and minimizing congestion in aisles. This can make it easier for operators to move through the warehouse without unnecessary backtracking.
8. Conduct Regular Forklift Training
• Train for Tight Spaces: Forklift operators should receive training that emphasizes the unique challenges of maneuvering in dense warehouse environments. Training should focus on precision handling, safe navigation of narrow aisles, and using the forklift's full capabilities to its advantage (such as load positioning and turning techniques).
• Refresher Courses: Periodic refresher courses are important to keep operators updated on the latest safety standards and best practices.
9. Maintain Forklift and Warehouse Equipment
• Regular Maintenance: A well-maintained forklift is easier to maneuver, especially in confined spaces. Ensure all components, including steering, brakes, and lift mechanisms, are in optimal condition.
• Inspect Warehouse Equipment: Ensure that shelves, racks, and other warehouse fixtures are stable and properly positioned. A poorly positioned shelf or rack can obstruct forklift movement and create safety hazards.
10. Implement Safe Pedestrian Practices
• Separate Pedestrian and Forklift Paths: In dense environments, keeping pedestrians and forklifts separated is critical. Mark designated walkways for personnel, and ensure that these paths don’t cross forklift routes unless absolutely necessary.
• Warn of Movement: Use horns, lights, or other warning systems to signal when a forklift is moving, especially in areas with poor visibility or high traffic. Pedestrians should always be aware of moving equipment.
11. Adopt Efficient Load Handling Practices
• Optimize Load Placement: Proper placement of goods can help reduce the need for forklifts to make extra trips or make complex maneuvers in narrow aisles. Load goods in a way that minimizes movement within the warehouse.
• Batch Picking: Implementing batch picking (where multiple items are picked in a single trip) can reduce the number of forklift movements and improve efficiency in tight spaces.
Operating a forklift in a dense warehouse requires careful planning, precise maneuvering, and a commitment to safety. By following these tips—such as optimizing forklift types, using spotters, maintaining safe distances, and ensuring clear communication—you can significantly improve efficiency while minimizing the risk of accidents. Forklifts remain an invaluable tool in modern warehouses, but their safe and effective operation is key to maintaining a productive and accident-free environment.
If you need further advice on improving forklift operations in tight spaces or implementing more advanced warehouse solutions, feel free to reach out.
Stay safe and efficient!