AUGUST 21, 2024
Royal Forklift Successfully Completes First On-Site After-Sales Training in Italy, Launching Efficient Collaboration with Naples Client
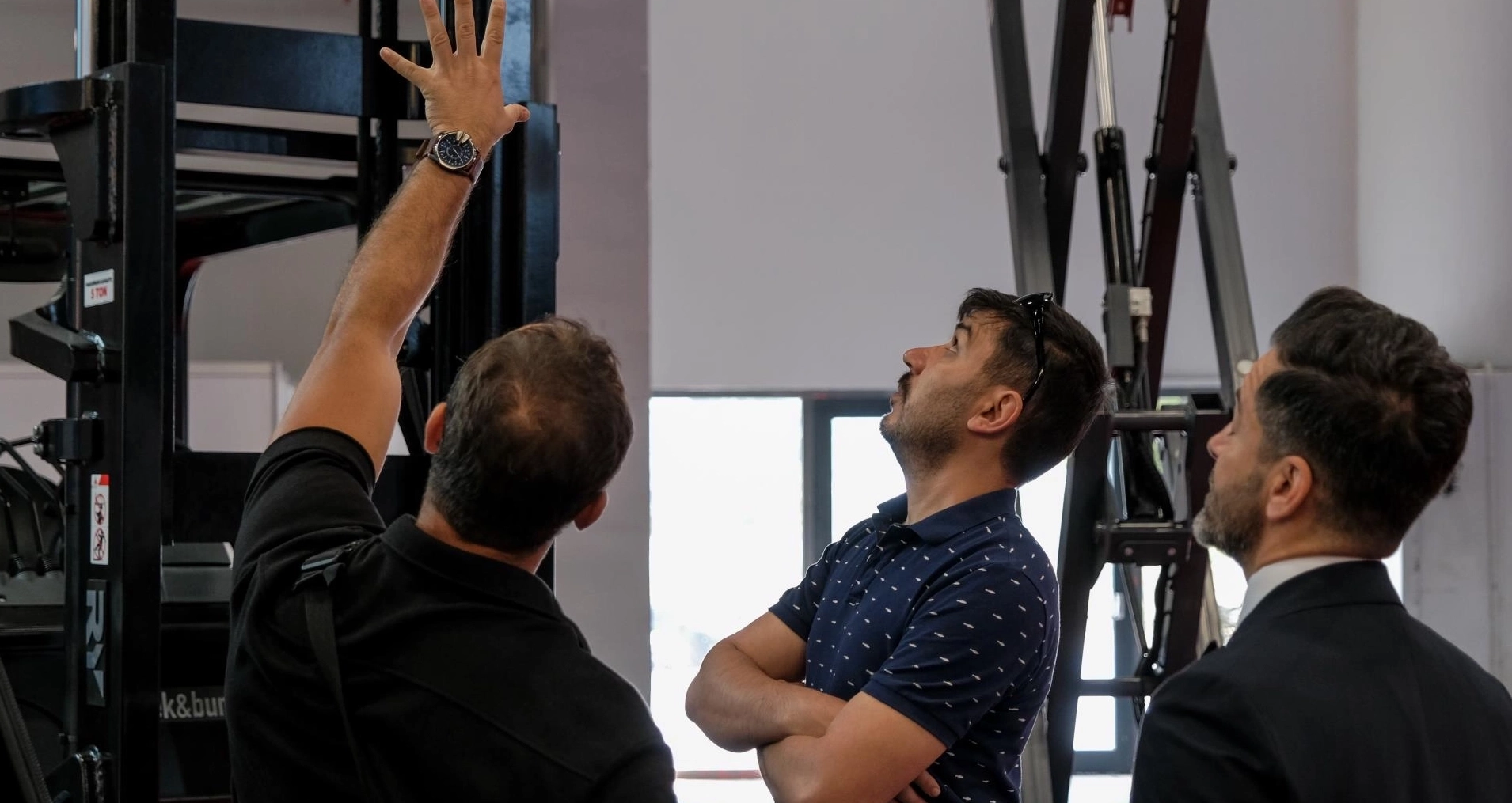
On October 27, 2024, Royal Forklift (Suzhou) Co., Ltd. successfully conducted its first specialized after-sales training for diesel forklifts at the premises of a logistics company in Italy. Led by Royal Forklift’s European market team, the training provided comprehensive guidance on the operation and maintenance of the newly purchased Royal Standard series diesel forklifts, marking the official start of a strategic partnership between the two parties.
Practical Training: Empowering Full-Cycle Operations and Maintenance
At the client’s warehouse, the Royal Forklift team focused on core scenarios for the 5-ton diesel forklift:
Precision Operation: Market expert Roy demonstrated cold-start techniques, load control on slopes (simulating the hilly terrain of port area), and the “micro-control mode” for navigating narrow aisles.
Safety Protocols: Emphasized load balance detection for the hydraulic lifting system and simulated emergency braking procedures in case of sudden failures.
Maintenance Practice:
Routine maintenance: A “20-minute quick process” for replacing oil filters and air filters.
Parts replacement: Demonstrated how to use QR codes on the forklift to access 3D disassembly animations, enabling the client’s engineers to replace brake pads independently.
After hands-on practice, the client team remarked, “This is ten times more intuitive than the manual! The slope anti-slip control demonstration perfectly matches our actual working conditions.”
Localized Service: Grounding Technology in Real-World Scenarios
To meet the high-intensity demands of Italy’s logistics industry, the training included customized content:
High-Temperature Operations: Explained the cleaning frequency of the diesel engine cooling system and lubricant viscosity selection for Southern Europe’s summer climate.
Cost-Saving Tips: Shared “Chinese expertise” such as filter cleaning for reuse and tire wear alerts to extend equipment lifespan. The client’s owner noted, “These details could save us tens of thousands of euros in maintenance costs annually.”
From Training to Collaboration: Seeds of Trust Planted
Following the training, a brief partnership launch ceremony was held. The client’s partner stated, “We’ve reviewed technical specs from many brands, but Royal Forklift’s willingness to fly here and teach us hands-on shows a level of sincerity that confirms we’ve chosen the right partner.” According to the agreement, Royal Forklift will provide:
24/7 Italian Remote Support: Real-time fault diagnosis via AR glasses.
Spare Parts Pre-Stocking Plan: Common parts will be stored in a bonded warehouse in EU to reduce repair downtime.
Looking Ahead: Deepening the European Service Network
Roy, Royal Forklift’s European Market Director, revealed, “This training is our first ‘technology training’ pilot in Southern Europe. In 2025, we will establish technical service centers in EU to truly integrate ‘Chinese innovation’ into Europe’s industrial chain.”